ニチアスは 「断つ・保つ」®の技術で
地球の明るい未来に貢献します
ニチアスは、「シール」「断熱」「防音」「耐火」「耐食」「クリーン」といった「断つ・保つ」®の技術を基盤とした5つの事業でさまざまな産業分野を支え、地球環境の保全に貢献しております。
各種プラント設備向けに製品やエンジニアリングを提供する「プラント向け工事・販売事業」をはじめ、基幹産業を主な市場とする「工業製品事業」、半導体産業に特化した「高機能製品事業」、自動車メーカーなどを主な客先とする「自動車部品事業」、ビルや住宅の建材を供給・施工する「建材事業」、いずれの事業もこれまでに培ってきた技術や経験を活かしながら、グローバル化を推進しています。
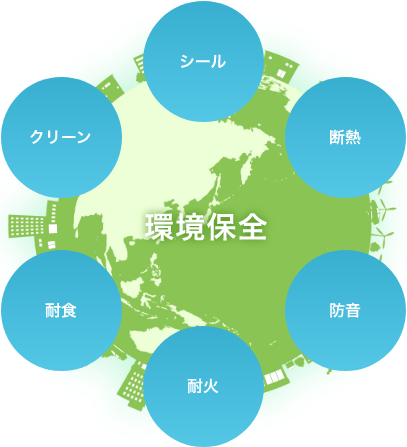
製品案内
Products Information
お知らせ
News
- すべて
- お知らせ
- 製品関連
- イベント
- マキベエ特設サイト開設のお知らせ
- ニチアスは、広島ドラゴンフライズをダイヤモンドパートナーとして応援します
- WEBセミナー講演のお知らせ【保温材の劣化が引き起こす熱ロス~Thermofit®で見逃さない~】
IR ニュース
IR News
会社案内
Company
サステナビリティ
Sustainability
お問い合わせ
Contact